Thanks to the experience gained from various retrofit projects and the combined expertise of our employees, we were able to develop a new control-system for the milling process and thus set a new benchmark in the industry. Thanks to improved operating and monitoring options, efficient process design and industry-specific analysis options, we are actively helping to increase the competitive edge of our customers.
ICS Automation AG
is working on automation projects worldwide and has a strong reputation in the food industry. We handle processes from raw material intake to the finished product and implement the necessary processes such as raw material transfer, tank storage and silo systems, dosing and mixing, etc.. More and more often, single machines or plant components are integrated into such production plants, which are then integrated into the production process by us. Therefore, we have expanded our know-how regarding interface engineering step by step in order to provide our customers with complete traceability throughout the entire process.
References
Control systems for Milling Industry
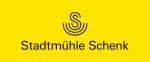
Buffer and conveying systems
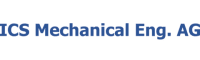
Together with our sister company ICS Mechanical AG we supply buffering, handling and conveying systems for the food and non-food industry worldwide.
Replacement process control systems
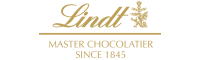
For almost 20 years, ICS Automation AG has been servicing various production plants worldwide for the manufacture of chocolate. ICS controls the process from the intake of the cocoa bean to the loading of the moulding equipment, which finally gives the chocolate the desired form.
Plant with product traceability
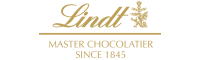
One of the main requirements for manufacturing companies is the traceability of production processes to ensure food safety, for example. The targeted division of the production process as well as the subdivision into defined production quantities (batches) form the foundation for this. Today's systems allow further possibilities and an almost complete evaluation of the production process.
Retrofit projects
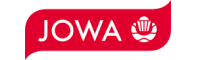
ICS has gained a lot of experience in various retrofit projects and, thanks to its team size, has the necessary resources to handle even larger retrofit projects.
Fiber cement plants
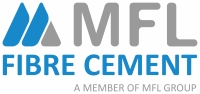
Together with MFL Faserzement GmbH, we work on fiber cement projects worldwide.
Dairies
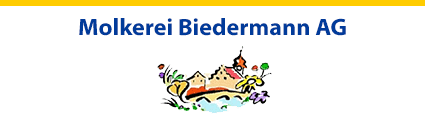
The company Molkerei Biedermann AG from Bischofszell is one of the first customers of ICS Automation AG. Thanks to the long-term partnership, the various projects can be implemented efficiently and without major downtimes.
Process optimization
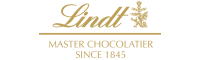
Thanks to the continuous exchange with our customers, we receive frequent requests to develop process optimizations with a focus on energy consumption, sustainability or minimization of downtime and waste.
Integration maintenance software
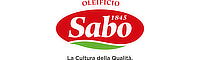
Many of our customers work with our process control system and process visualization every day. By displaying and analyzing of all the controlled elements, the user always has an overview of his production processes as well as the status of the plants.